What is silicone rubber? Silicone rubber refers to a rubber whose main chain is composed of alternating silicon and oxygen atoms, and the silicon atom is usually connected to two organic groups. Ordinary silicone rubber is mainly composed of siloxane chains containing methyl and a small amount of vinyl. The introduction of phenyl can improve the high and low temperature resistance of silicone rubber, while the introduction of trifluoropropyl and cyano can improve the heat and oil resistance of silicone rubber. Silicone rubber has good low temperature resistance and can generally still work at -55℃. After the introduction of phenyl, it can reach -73℃. The heat resistance of silicone rubber is also outstanding. It can work for a long time at 180℃, and can withstand several weeks or more at a temperature slightly higher than 200℃ and still be elastic. It can instantly withstand high temperatures above 300℃. Silicone rubber has good air permeability and the oxygen permeability is the highest among synthetic polymers. In addition, silicone rubber also has the outstanding characteristics of physiological inertness and does not cause blood coagulation, so it is widely used in the medical field.
Among the various types of rubber used, rubber used to make tires accounts for more than half of the consumption of all rubber raw materials, and the rest is used for non-tire products. In terms of various types of rubber, natural rubber is still the leader, accounting for about 41%, styrene-butadiene rubber and butadiene rubber account for about 28% in total, and the amount of silicone rubber, as organic silicone polymer elastomers have many unique and valuable properties, such as high and low temperature resistance, weather resistance, aging resistance, electrical insulation, ozone resistance, hydrophobicity, physiological inertness, etc., which are incomparable and irreplaceable by other organic polymer elastomers. It has been widely used in aerospace, medical and health, electronics and electrical, industry and agriculture, transportation and daily necessities, and has become an important and indispensable new rubber material in the national economy.
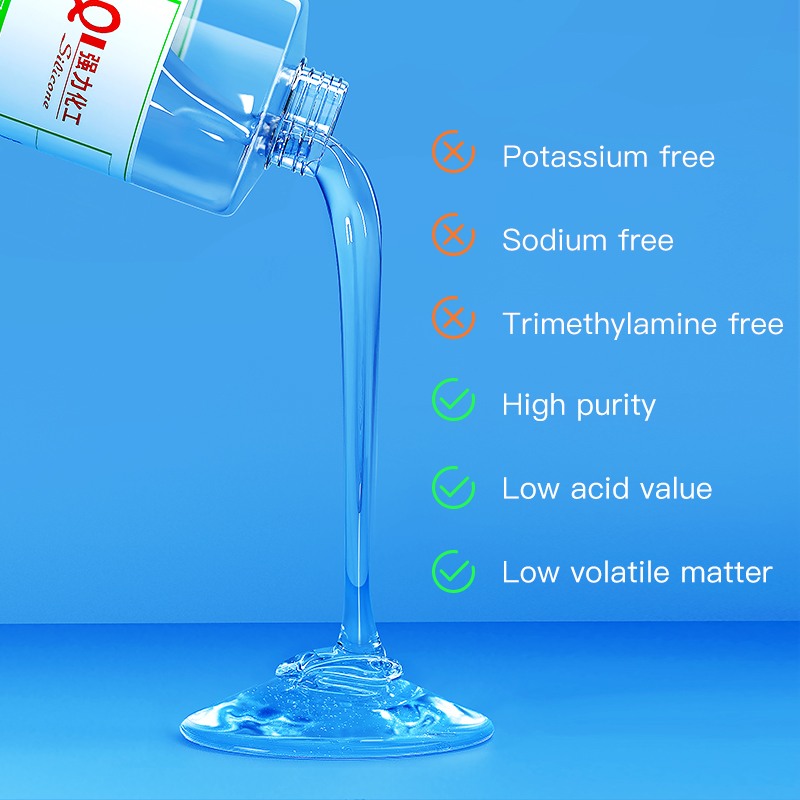
The development of the silicone rubber industry has led to the expansion and popularization of the production scale of silicone monomers due to the large demand for downstream products. The production of silicone rubber has gradually changed from technology control to cost control of bulk industrial rubber materials. Silicone rubber production belongs to the category of coal-to-rubber, which refers to the production of silicone rubber with coal as the main raw material and fuel. In the case of supporting thermal power equipment, with coal and quartz sand as the starting raw materials, every ton of silicone rubber produced requires ten tons of coal (equivalent to 5000 kcal thermal coal). Roughly speaking, the price of one ton of silicone rubber is 20,000 yuan, so the price of coal has a decisive influence on the cost of silicone rubber. This forces us to work hard on the synthesis route, energy consumption and efficiency improvement in order to compare with other synthetic rubbers.
Due to the rapid development of silicone rubber applications and promising prospects, it is expected that in the next ten years, the demand and consumption of silicone rubber will reach more than 2.5 million tons, accounting for about 20% of the total demand for rubber. Under such a development trend, it will greatly promote the upstream and downstream industries of silicone rubber production. For the upstream, it will promote the high-tech finishing of the coal industry, make full use of my country's abundant coal resources, learn foreign advanced synthesis technology, and strive to improve the self-sufficiency rate of silicone rubber. At present, some high-quality silicone rubber still relies on foreign companies such as Dow Corning and Wacker for supply. For the downstream, it is necessary to develop silicone rubber and other rubber blends, take advantage of the advantages and disadvantages of the performance of silicone rubber and other different rubbers, learn from each other's strengths and weaknesses, eliminate the weaknesses of a single material, and obtain a blended rubber with relatively ideal comprehensive performance. Follow the principle of similar polarity, similar solubility parameter, similar viscosity, similar surface tension, and the principle of synchronous balance of the co-vulcanization speed of the blended rubber to realize the process technology of silicone rubber blending with other rubbers. The more mature co-blending process is to use the method of adding silane coupling agent or graft polymerization process to blend silicone with other rubbers. For example, when blended with EPDM rubber, the blended rubber has both the unique properties of silicone and the weather resistance, ozone resistance and chemical resistance of EPDM rubber. This blended rubber is widely used in rubber parts of automobiles. Now, silicone rubber and acrylate rubber are blended, and high molar mass long-chain alkyl silicone oil is added to the blended rubber as a compatibilizer, or hydrogen-containing silicone oil is added and then chloroplatinic acid is added to catalyze the mixture to form a silane hydrogen addition reaction to obtain a blending effect, taking advantage of the excellent oil resistance of acrylate to make the two properties complementary.
With the rapid development of the silicone rubber industry, the research and development, production and promotion of silicone rubber in developed industrial countries have entered a new stage of comprehensive development. Silicone rubber that does not require secondary vulcanization, silicone rubber that can be vulcanized at 100 degrees Celsius, and silicon-nitrogen rubber that can withstand high temperatures of 300 degrees Celsius have formed industrialized production, and more silicone rubber varieties have been applied to different fields. Although my country's silicone rubber industry started late, it has made great progress in product types and production processes. I believe that my country's silicone rubber industry will develop faster and better in the future.
The text and pictures in this article are from the Internet, encyclopedias, etc., and are only for learning and communication among interested colleagues in and outside the industry. If there is any infringement, please contact us to delete it.