1) What is foam
2) Causes of foam
(1) Use of surfactants;
(2) Use of polymer compounds;
(3) It has a certain defoaming ability, but the foaming speed is greater than the defoaming speed;
(4) Because the system is thick and stirring is used during production or processing, bubbles will be generated due to the entry of air;
(5) When the system itself undergoes a chemical reaction, some gas molecules are generated. This process is sometimes also called degassing or aspiration process.
3) Why defoaming
(1) It causes the reaction materials to overflow the reactor, causing waste of raw materials and reducing production capacity;
(2) Due to insufficient collision between raw materials, the reaction cycle is extended;
(3) It causes a decline in product quality;
(4) It causes passive operation and the generation of foam makes it impossible to carry out normal production.
Defoaming mechanism
The surface tension of the defoaming agent is low, and it is easy to enter the liquid film and expand, reducing the surface tension of the liquid film, making the liquid film gradually thinner, uneven internal force, and losing its self-repairing ability, resulting in its rupture.
Classification, characteristics and composition of defoamers
1) Classification
Organosilicon defoamers, polyether defoamers, mineral oil defoamers, fatty alcohol defoamers, solid defoamers
2) Characteristics
Polyether defoamers have excellent properties such as strong antifoaming ability and high temperature resistance. The disadvantages are that they are toxic to a certain extent, the conditions of use are limited by temperature, the foam breaking rate is not high, and the application field is narrow. The common glycerol polyether defoamers on the market can be roughly divided into GP type-polyoxypropylene glycerol polyether, GPE type-polyoxypropylene polyoxyethylene glycerol ether and GPES type-polyoxypropylene polyoxyethylene glycerol polyether ester.
Organosilicon defoamers are liquids with particularly low surface tension containing polysiloxane as their main active ingredient. At the same time, fillers such as silica are added to form the main defoaming components, which can be prepared into emulsion defoamers and solid defoamers. Its basic characteristics are stable chemical properties, wide range of use, low volatility, non-toxicity, and outstanding defoaming ability. The disadvantage is poor antifoaming performance.
3) Composition
Active ingredient - the most important core part, plays a role in breaking bubbles and reducing surface tension;
Representatives: silicone oil, polyethers, higher alcohols, mineral oil, vegetable oil, etc.
Emulsifier - disperses the active ingredient into small particles so that it can be better dispersed into oil or water, and has a better defoaming effect;
Representatives: nonyl (octyl) phenol polyoxyethylene ether, soap salt, OP series, Tween series, Span series, etc.
Carrier - accounts for a large proportion of defoamers, its surface tension is not high, mainly plays the role of supporting medium, is beneficial to the defoaming effect, and can reduce costs;
Representatives: solvents other than water, such as aliphatic hydrocarbons, aromatic hydrocarbons, oxygen-containing solvents, etc.
Emulsifying aid - makes the emulsification effect better.
Representatives: dispersant: hydrophobic silica, etc.; thickener: CMC, polyethylene ether, etc.
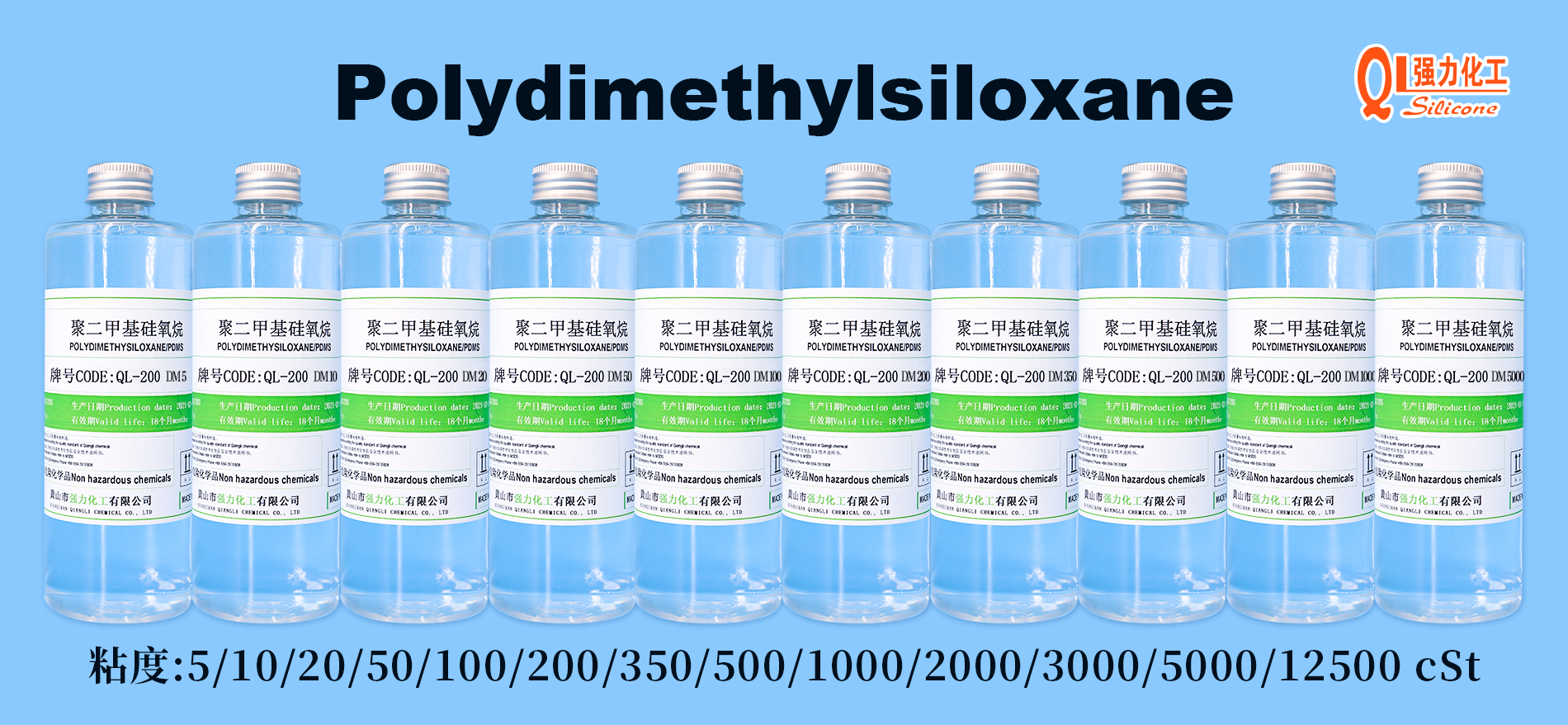