I. Analysis of potential causes of compatibility problems
1. Compatibility differences in chemical structure
Nitrile rubber characteristics: The main chain of NBR is a butadiene-acrylonitrile copolymer, the nitrile group (-CN) is highly polar, and it is resistant to non-polar oils (such as mineral oil), but it may be sensitive to polar solvents or substances containing siloxane.
Dimethyl silicone oil characteristics: The main chain is - Si-O - bond, the side group is a non-polar methyl group (-CH₃), and it is chemically inert, but the molecular weight, end group structure (such as hydroxyl end-capping) or additives (such as antioxidants, surfactants) may affect compatibility.
Potential reactions:
Silicone oil may slowly swell NBR, resulting in rubber volume expansion and decreased mechanical properties (such as decreased tensile strength and elasticity).
If the silicone oil contains acidic/alkaline impurities or catalyst residues (such as platinum, peroxide), it may catalyze the degradation of the NBR cross-linked structure or induce oxidation reaction.
2. Physical effect: swelling and migration
Swelling mechanism: As a low molecular weight substance, silicone oil may penetrate into the cross-linked network of NBR, destroy the intermolecular force, and cause the rubber to soften or swell (in accordance with the principle of "like dissolves like". Although NBR has strong polarity, low molecular weight silicone oil may still have some penetration).
Plasticizer migration: If the NBR formula contains plasticizers (such as phthalates) that are more compatible with silicone oil, "anti-plasticization" may occur, causing the plasticizer to migrate out and the rubber to become hard and brittle.
3. Influence of formula additives
Additives in silicone oil: such as antioxidants (amines, phenols), stabilizers, pigments, etc. may react chemically with vulcanizers (such as sulfur, peroxides) and accelerators (such as thiazoles, thiurams) in NBR to form precipitates or cause interface defects.
Compounding agents in NBR: the dispersibility of the vulcanization system (especially sulfur-containing vulcanizers) and fillers (such as carbon black and white carbon black) may affect the penetration path of silicone oil. If the filler surface is not treated, it may become a silicone oil adsorption site.
4. Influence of experimental conditions
Temperature and time: High temperature (such as > 100°C) will accelerate molecular movement and intensify swelling or chemical reactions; long-term contact may lead to gradual performance changes (the difference between short-term contact and long-term aging needs to be distinguished).
Contact method: The purity (whether it contains impurities), viscosity (low-viscosity silicone oil penetrates faster), and liquid surface coverage area of silicone oil in the immersion experiment may affect the repeatability of the results.
Sample pretreatment: Release agents on the surface of NBR (such as silicone oil release agent residues) may interfere with the experiment and need to be cleaned and dried with solvents (such as acetone).
2. Experimental optimization and troubleshooting steps
1. Basic performance characterization and standard testing
Test indicators (refer to ASTM D471 "Volume expansion and physical property changes of rubber in liquid"):
Mass change rate (Δm%): reflects silicone oil absorption or component migration.
Volume change rate (ΔV%): evaluates the degree of swelling (positive values indicate swelling, negative values may indicate shrinkage or plasticizer migration).
Mechanical properties: tensile strength, elongation at break, hardness change (if the hardness increases, it may be due to plasticizer loss, and if it decreases, it may be due to swelling).
Micromorphology: Scanning electron microscopy (SEM) is used to observe surface cracks and precipitates; infrared spectroscopy (FTIR) is used to analyze interfacial chemical changes.
Control group setting: pure dimethyl silicone oil (no additives) and NBR standard sample (known formula) are used for comparative experiments to eliminate interference from formula differences.
2. Variable control and one-by-one troubleshooting
Silicone oil parameters:
Replace silicone oils of different molecular weights (such as 50cs, 100cs, 1000cs). High-viscosity silicone oils have weaker penetration ability and may improve compatibility.
Use silicone oils with no active groups at the end (such as methyl end-capping to avoid the polar effects of hydroxyl/amino end-capped silicone oils).
Test "pure silicone oil" vs. "silicone oil with additives" to confirm whether the problem is caused by additives (such as switching to food-grade or medical-grade silicone oils to reduce impurities).
NBR formula adjustment:
If the NBR used in the experiment is homemade, check the degree of vulcanization (under-sulfurization may result in low cross-linking density and easy swelling).
Reduce the amount of polar plasticizers, or use plasticizers that are more compatible with silicone oil (such as trimellitic acid esters).
Add anti-migration agents (such as clay, silica fillers) or coupling agents (such as silane coupling agents) to improve interfacial bonding.
3. Environment and process optimization
Temperature gradient experiment: Test at room temperature (25℃), medium temperature (70℃), and high temperature (150℃) to determine the critical temperature of compatibility.
Contact mode adjustment: Change "complete immersion" to "surface coating" to observe whether the problem only occurs in the interface area (excluding the influence of internal penetration).
Pretreatment steps: NBR samples are fully aged after vulcanization (such as 70℃×24h) to remove residual vulcanizers; silicone oil is filtered or distilled before use to remove impurities.
III. Possible solutions
1. Material selection adjustment
If nitrile rubber must be used, NBR with a high acrylonitrile content (such as > 40%) is preferred, which has a higher crosslinking density and better swelling resistance.
If the compatibility problem cannot be solved, consider alternative rubbers: silicone rubber (VMQ, the same system as silicone oil, excellent compatibility), fluororubber (FKM, strong chemical resistance but high cost).
2. Silicone oil modification or surface treatment
Add a compatibilizer (such as nitrile-containing siloxane copolymer) to the silicone oil to improve the interfacial affinity by matching polar groups.
Silanize the NBR surface to form a transition layer to reduce silicone oil penetration.
3. Experimental standardization and data recording
Develop a detailed SOP to record the silicone oil brand/model, NBR formula, vulcanization conditions (temperature/time/pressure), test cycle, environmental parameters (humidity, light), etc. for each experiment to facilitate reproduction and analysis.
Use the orthogonal test method (L9 orthogonal table) to design multi-factor experiments and quickly locate key influencing factors (such as silicone oil viscosity, temperature, contact time).
IV. Summary
The compatibility problem between dimethyl silicone oil and NBR needs to be gradually investigated from "chemical compatibility → physical swelling → additive interaction → experimental conditions". Priority should be given to quantifying performance changes through standard tests, clarifying the type of problem (swelling, hardening, precipitation, etc.), and then adjusting the silicone oil model, NBR formula or experimental process in a targeted manner. If long-term contact is required in actual applications, it is recommended to select a commercial combination with verified compatibility (such as a specific brand of medical-grade silicone oil and industrial-grade NBR) and supplement it with long-term aging tests (such as 1000h life simulation).
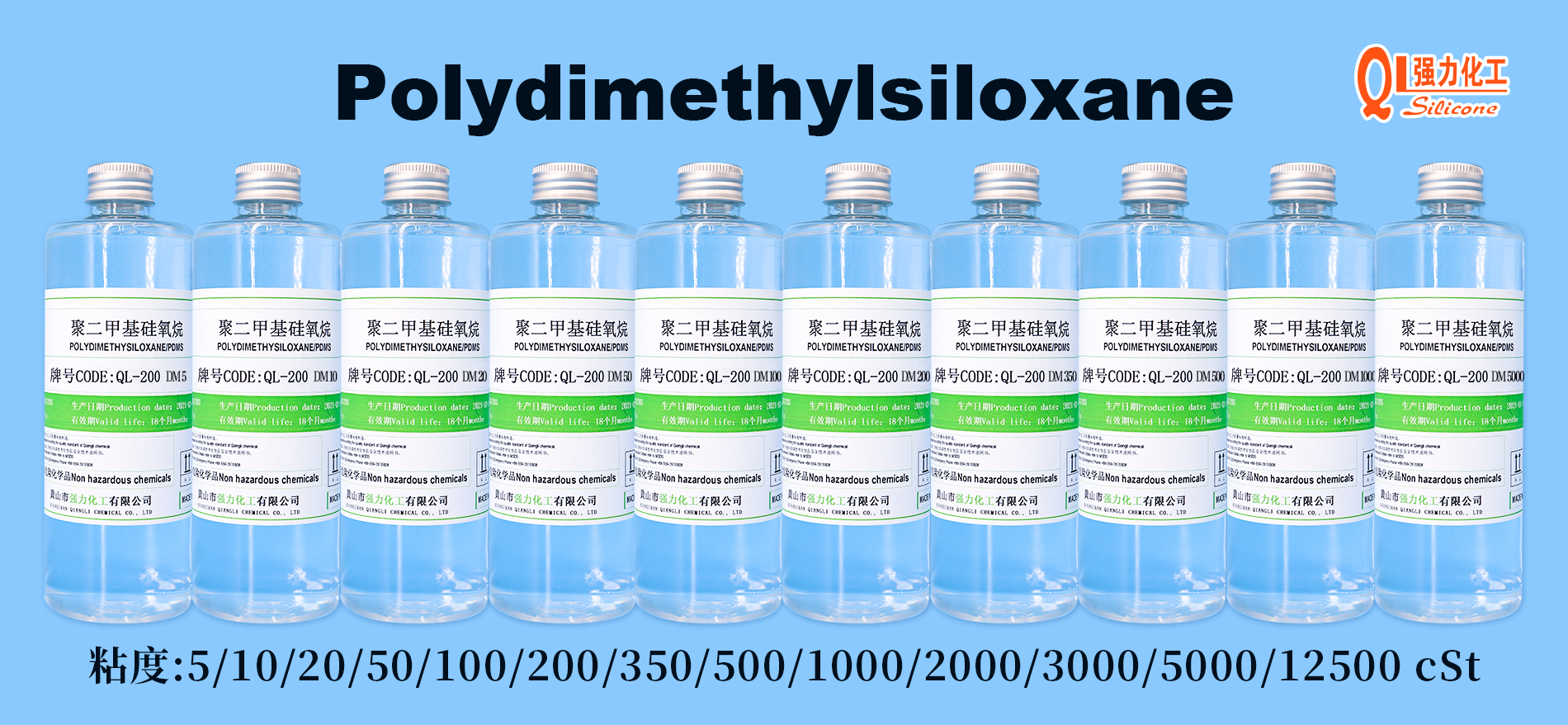