Silicone rubber foam material (also known as: silicone foam/foamed silicone) is made of silicone rubber raw rubber, fillers, vulcanizing agents, foaming agents, etc., and other auxiliary raw materials are added and mixed evenly, and then foamed at high temperature. A porous, low-density, compressible polymer elastomer material prepared by foam vulcanization. Nowadays, silicone rubber foam is increasingly widely used because it has the excellent properties of both silicone rubber and foam materials. Silicone foam has the high elasticity of rubber, and also has the sound-absorbing, sound-insulating, shock-absorbing and buffering properties of foam materials. It is mostly used for shock-absorbing pads, sealing pads, sound insulation materials, insulation materials, aviation thermal insulation materials and other material properties. Occasions with relatively high requirements.
1. General properties of silicone rubber
Silicone rubber has many excellent properties:
(1) High and low temperature resistance
Silicone rubber has excellent mechanical properties in high temperature (above 200°C) environments and still has a certain degree of toughness and elasticity. The glass transition temperature (Tg) can be as low as -70 ℃. Generally, the working temperature of silicone rubber is -100 ℃ to 350 ℃. It can withstand instantaneous high temperatures of thousands of degrees, so it is often used to make heat-resistant coatings, such as in the aviation field.
(2) Electrical insulation
Silicone rubber has good insulation properties. After burning, the silica produced is still an insulating substance. In addition, silicone rubber is not easily scorched during arc discharge because it has fewer carbon atoms in its structure and its reinforcing filler silica is suitable for high-voltage applications.
(3) Physiological inertia
The surface of silicone rubber is hydrophobic, so the physical properties decrease little in humid environments. Poor adhesion, can play a role in isolation. It is non-toxic and tasteless, does no harm to human health, and can only react slightly with the body, which results in its excellent physiological inertness. At the same time, it is also very superior in terms of physiological aging performance.
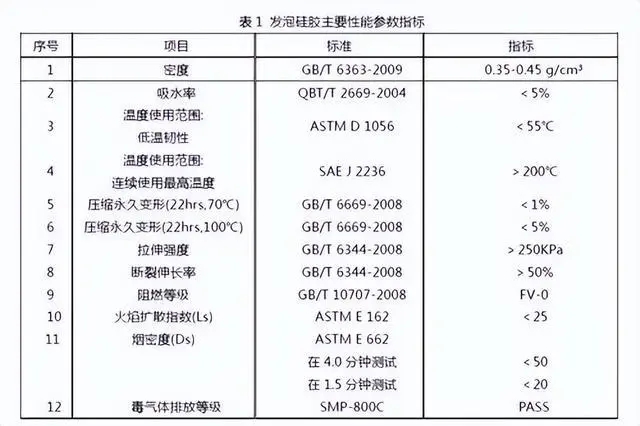
2. Characteristics of organic silicone foam materials:
Silicone foam is increasingly widely used because it has the excellent properties of both silicone rubber and foam materials. It not only has the high resilience and aging resistance of rubber, but also has the properties of foam such as sound absorption and shock absorption. It is mostly used for waterproofing. , shock absorption, gaskets, sound insulation, insulation, aviation thermal insulation and other situations with relatively high performance requirements. According to the cell structure, silicone rubber foam is divided into three types: closed cell type, open cell type and mixed type. Closed-cell foamed silicone foam materials have good shock-proof buffering, sound insulation, heat insulation, flame retardant and explosion-proof properties. In the automotive field, they are mainly used for insulating foam pipes for automotive air conditioners, automotive shock absorption, and new energy. Foamed silicone sealing gaskets for automobile batteries, etc.
Today, many automobile interior materials, such as floors, ceilings, steering wheels, car seats, etc., are made of polyurethane foam materials. On the one hand, the technology of polyurethane foam materials is relatively mature and its performance meets the usage standards; on the other hand, it is Because polyurethane foam materials are cheaper. However, polyurethane foam materials have poor weather resistance, are flammable, and release a large amount of toxic gases that are harmful to the human body during combustion. Therefore, with the promotion of organic silicone foam materials and the improvement of people's understanding of them, organic silicone foam materials are expected to replace traditional polyurethane foam materials in the future.
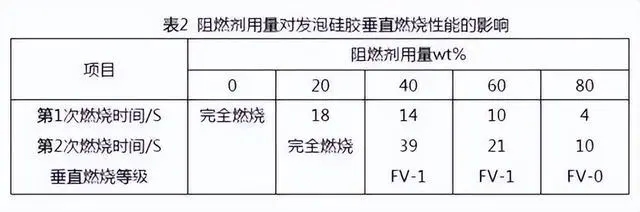
2.1 Density selection of foamed silicone
The density of the silicone rubber matrix is 1.17g/cm3. However, through foaming treatment, the density of silicone rubber foam materials prepared in the current mature process can be as low as 0.16-0.20 g/cm3, and can be used in car seats, headrests and other components; while conventional silicone rubber Foam materials (density 0.45 g/cm3) are widely used for gap filling in sealing, shock absorption and other parts.
2.2 Flame retardant properties of foamed silicone
One of the test methods commonly used to characterize the flame retardant properties of polymers is the vertical combustion method. Its combustion mode is very close to the actual situation of object burning, so it can well reflect the actual flame retardant effect of silicone rubber. The effect of flame retardant dosage on the vertical combustion performance of silicone rubber is shown in Table 2. As can be seen from Table 2, silicone rubber without flame retardant burns completely; silicone rubber with 40 parts of flame retardant added has a vertical combustion grade of FV-1 and has a certain self-extinguishing ability; silicone rubber with 80 parts of flame retardant added The vertical combustion grade of silicone rubber has even reached FV-0 level, showing good self-extinguishing properties.
2.3 Electrical insulation properties of foamed silicone
As the amount of physical filler increases, the volume resistivity and surface resistivity of silicone rubber show a decreasing trend, and the dielectric constant and dielectric loss factor generally show an increasing trend. It can be seen that adding physical fillers damages the electrical insulation properties of silicone rubber to a certain extent.
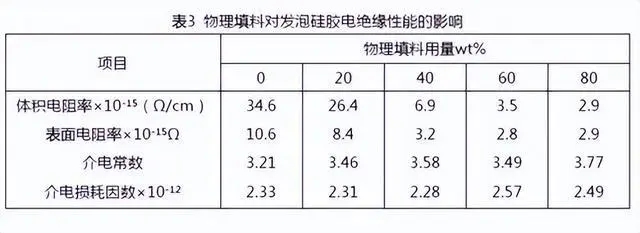
The key technology of new energy electric vehicles lies in the sufficient charging technology and performance of the high-energy-density lithium batteries of electric vehicles. Lithium batteries must maintain strict waterproof and dustproof requirements during use, and the tendency to heat and spontaneously ignite is the number one problem affecting the use of electric vehicles. In order to meet the requirements for sealing and buffering protection of power batteries during driving in heavy rain, shoals, haze and other conditions, organic silicone foam materials can be applied to power batteries. Use silicone foam potting material to protect individual cells. Silicone foam is also widely used to prevent light leakage, prevent dust, absorb shock, and increase air tightness around car lights; as well as to prevent noise and fill gaps around electric car horns and speakers.
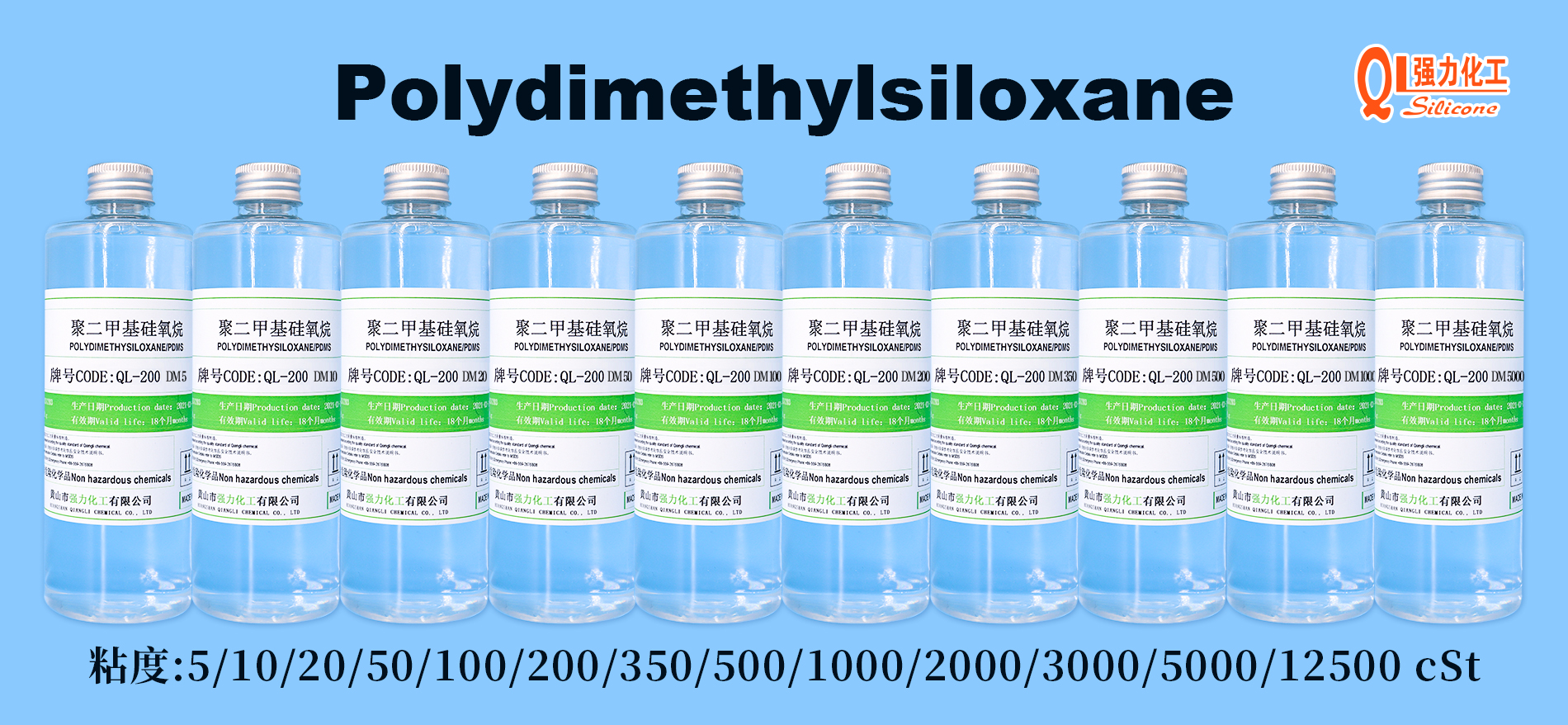