Recently, many customers have asked about silicone rubber, and have also discussed a lot about base materials, fillers, formulas and the like. The editor has collected some information and sorted out the types of silicone rubber for your study and reference.
Dimethyl silicone rubber
Dimethyl silicone rubber is the earliest silicone rubber put into commercial production. It can maintain good elasticity in the range of -60 to 200°C, has good aging resistance, has excellent electrical insulation properties, moisture resistance, shock resistance, and physiological inertness. characteristic.
Dimethyl silicone rubber is mainly used for fabric coating, and can also be made into various extruded and calendered products for use in electromechanical, aviation, automotive, medical and other industries. However, due to the low vulcanization activity of dimethyl silicone rubber, it is difficult to vulcanize when used to manufacture thick products, the inner layer is prone to blistering, and the high-temperature compression permanent deformation is large, so it has been replaced by methyl vinyl silicone rubber.
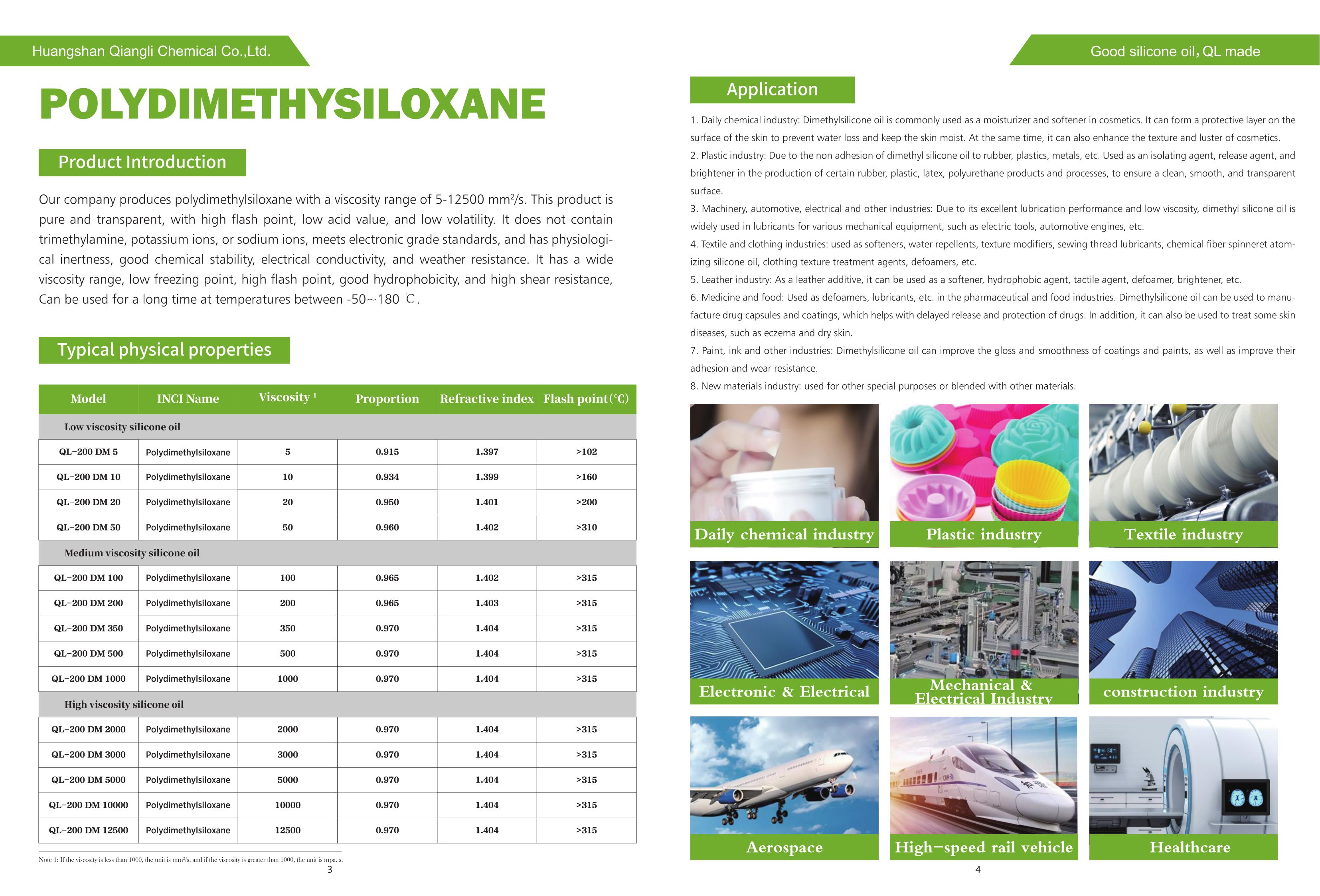
Since the introduction of a small amount of vinyl into the macromolecular structure of silicone rubber can greatly improve the vulcanization processing performance of silicone rubber, most of the silicone rubber currently used contains vinyl. Methyl vinyl silicone rubber is the most versatile silicone rubber and currently dominates the production of silicone rubber at home and abroad. Because it introduces partially unsaturated vinyl groups on the side chains, its processing performance and physical and mechanical properties are better than those of two-based silicone rubber. In addition to the general characteristics of dimethyl silicone rubber, it also has a wide operating temperature range and can maintain good elasticity in the range of -60 to 260°C. It is easier to vulcanize than dimethyl silicone rubber and has a smaller compression permanent deformation, better resistance to solvent expansion, stability to high-pressure steam, and excellent cold resistance, etc., and because of the use of less active peroxides for processing
It is vulcanized, thereby reducing the weaknesses of bubbles and poor rubber stability during vulcanization. Therefore, methyl vinyl silicone rubber can generally be used to make thicker products.
Methyl vinyl silicone rubber is the most widely used variety of silicone rubber. Various high-performance and special-purpose silicone rubbers that have emerged in recent years are mostly based on vinyl silicone rubber, such as high-strength silicone rubber, low-density silicone rubber, etc. Compression permanent deformation silicone rubber, no post-vulcanization silicone rubber, heat-resistant conductive silicone rubber and medical silicone rubber, etc. In the aviation industry, methyl vinyl silicone rubber is widely used as gaskets, sealing materials and protective layers for fragile and shock-proof components; in the electrical industry, it can be used as advanced insulating materials for electronic components and dynamic sealing rings for high-temperature potentiometers. Seals for underground long-distance communication equipment; in medicine, because methylvinyl silicone rubber has little physiological reaction to the human body and is non-toxic, it is used in plastic surgery, artificial heart valves, blood vessels, etc.
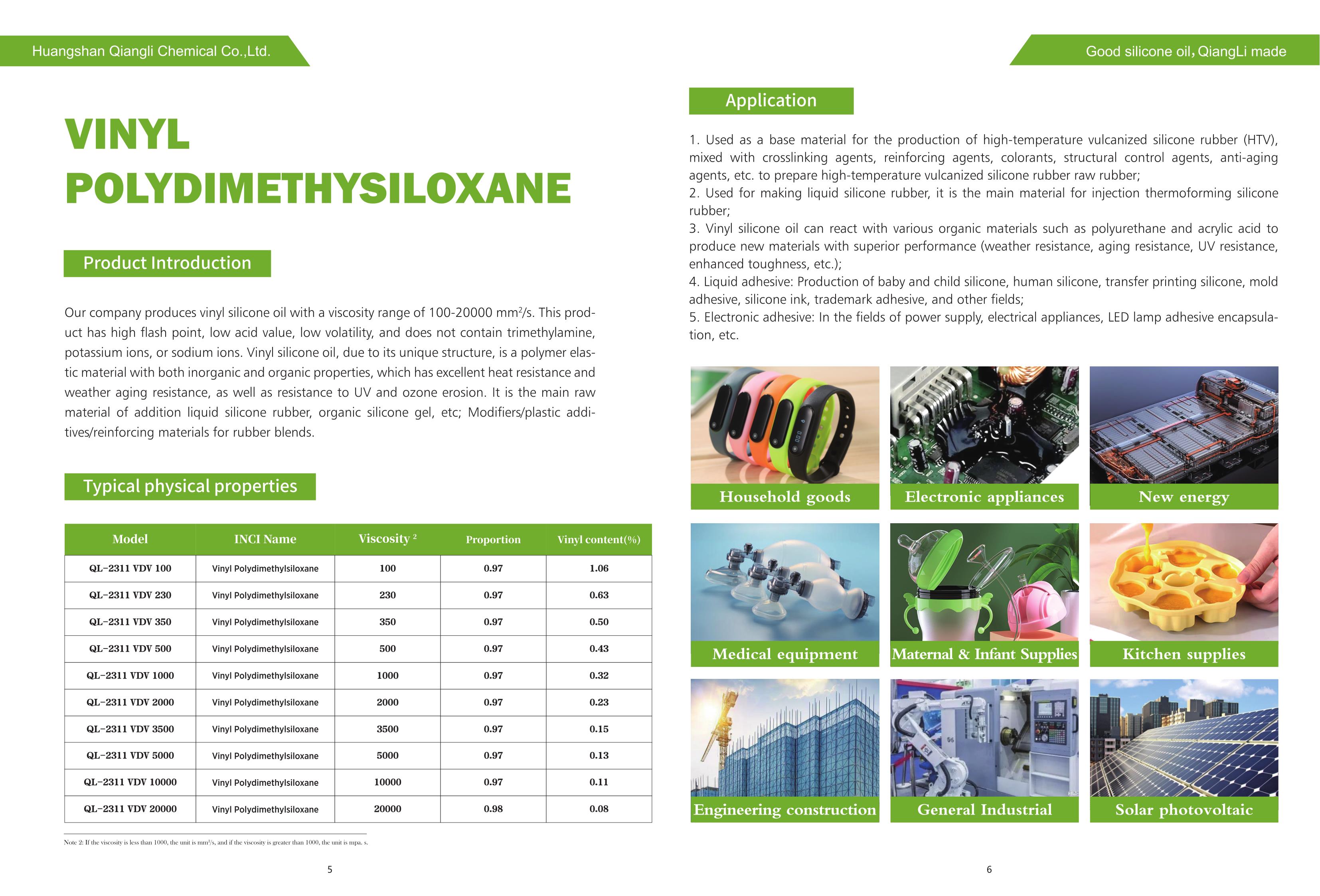
Diethyl silicone rubber, which is made by introducing ethyl groups into polysiloxane side chains, has particularly good cold resistance, and its cold resistance is better than dimethyl silicone rubber and general methylvinyl silicone rubber. The higher the ethyl content, the better the cold resistance. However, the reactivity of ethyl group is greater than that of methyl group. Therefore, as the ethyl group content increases, the heat resistance decreases. As an ethyl silicone rubber for low-temperature use, it is appropriate to contain 8 mol% of diethyl silicone chain segments in the polymer. The service temperature of ethyl silicone rubber is generally -70~200℃.
The main advantage of silicone rubber is its excellent thermal stability. It does not decompose at 430~480℃, and some can even withstand high temperatures above 500℃. The outstanding weakness of silicone rubber is its poor hydrolytic stability, and it was once considered to have no future. Later, it was discovered that polymers with cyclodisilazane introduced into the main chain have good thermal stability. The cyclodisilazane-containing elastomer modified with silarylene does not lose weight when heated to 425°C in air, and loses only 10% at 570°C, and has good hydrolysis stability.