In the production process of many industries (such as printing and dyeing, fermentation, papermaking, paint, medicine, oil field exploitation, water treatment, etc.), a large amount of foam is often generated due to operations such as stirring, vibration, and boiling. Production brings a lot of troubles, such as affecting the normal production, reducing the effective load of equipment, resulting in a decline in product quality and production capacity, etc. In order to eliminate and suppress foam, the most effective and most economical and convenient way is to add defoamers. The following is a brief Introduce the factors affecting the performance of defoamers.
Defoamer, also known as antifoaming agent, can be divided into oily, emulsion, solid and paste according to the state; according to the chemical composition, it can be divided into alcohols, fatty acids, amides, phosphates, polyethers and polysilicon Oxanes (also known as organic silicon) and so on. Compared with non-silicon defoamers, silicone defoamers have attracted attention from all walks of life because of their good defoaming and foam suppression effects and less dosage.
1. Effect of viscosity and dosage of methyl silicone oil on performance of defoamer
Methyl silicone oil has low surface tension, strong defoaming ability, good thermal stability, chemical and physiological inertness, and is insoluble in water. It has excellent defoaming performance for most foaming media. Therefore, we choose methyl silicone oil as One of the main components of the defoamer. With other conditions kept constant, the influence of the viscosity change of the methyl silicone oil on the performance of the defoamer was investigated. The experimental results: with the increase of the viscosity of the methyl silicone oil, the defoaming time of the defoamer decreased first. Then it tends to increase slightly, but the antifoaming time has been increasing. This is because the low-viscosity methyl silicone oil has a small surface tension and is easy to disperse in the foaming liquid to play a defoaming effect, but the solubility is large and the antifoaming time is short; while Methyl silicone oil with high viscosity has low solubility and long antifoaming time, but it is difficult to emulsify and has poor defoaming effect.
In addition, the content of methyl silicone oil in the emulsion should also be moderate. If the amount is too low, the defoaming effect will be poor. In order to achieve the expected defoaming effect, the amount of defoaming agent emulsion must be added, but this will affect the product quality ; If the amount is too high, it will not be easy to emulsify. Experiments show that the appropriate content of methyl silicone oil in the emulsion is 16%-17%.
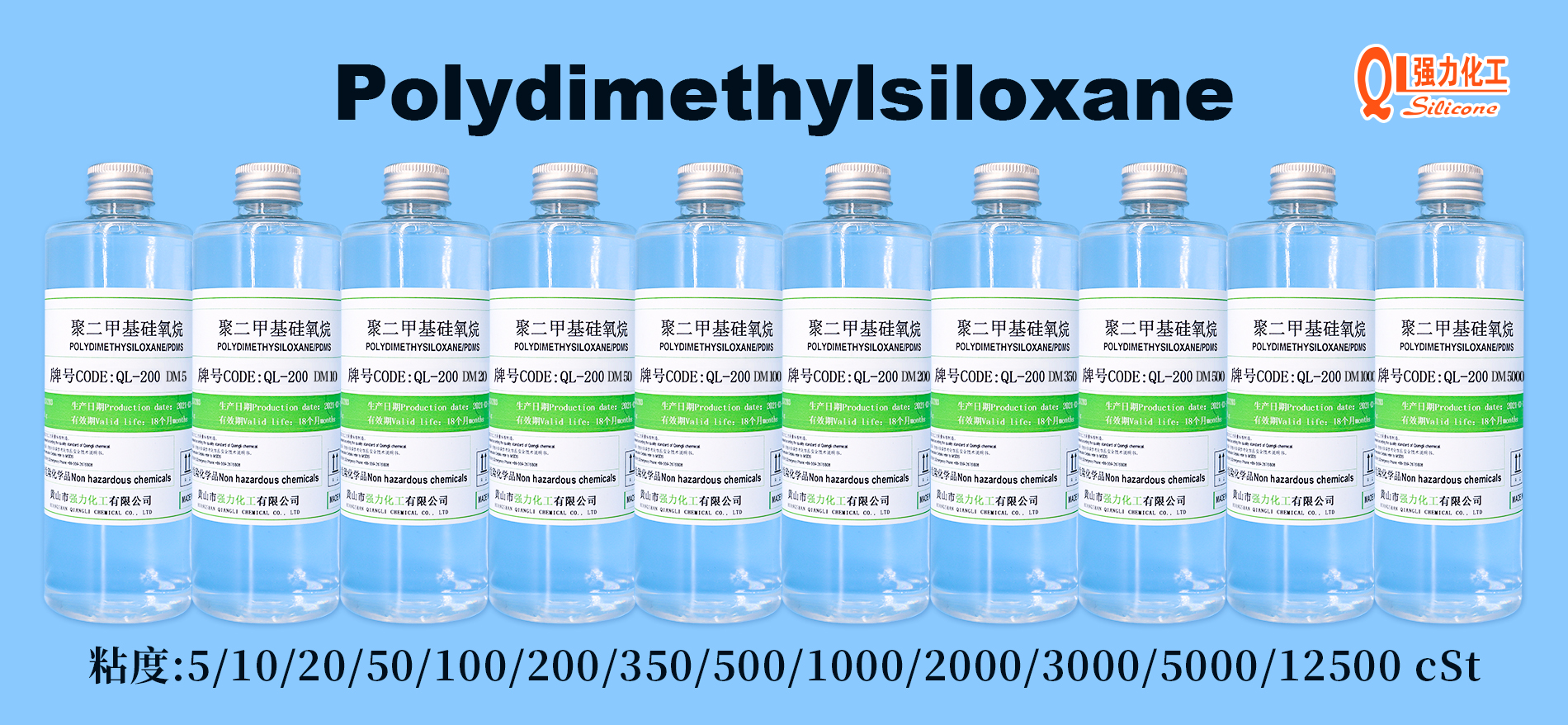
Silica that can be used for methyl silicone oil defoamer includes: fumed silica, precipitated silica, silica gel, silica sol and quartz powder, etc. Due to the large specific surface area and low density of fumed silica (white carbon black), Easy to disperse, hydrophilic without hydrophobic treatment, difficult to infiltrate and disperse in the organic phase, after hydrophobic treatment, the content of substrates on the surface decreases, the aggregation tendency weakens, the surface whiteness decreases, and it changes from hydrophilic to hydrophobic. The wettability and dispersibility of the organic phase are improved, which helps to enhance the dispersibility of silicone oil in the foaming system and increase the stability of the emulsion! Therefore, we choose fumed silica and methyl silicone oil for compounding to improve Defoaming effect of methyl silicone oil.
Under other conditions being the same, investigate the influence of different dosages of white carbon black on the defoaming performance of the defoamer, as shown in the experimental results. With the increase of the dosage of white carbon black, the stability of the obtained defoamer emulsion becomes worse. Relative to 100 In terms of g methyl silicone oil, when the amount of silica is less than 8g (equivalent to the amount of silica in the emulsion is 1.300), with the increase of the amount of silica, the defoaming performance of the defoamer is enhanced, but when the silica When the dosage is higher than 89%, its defoaming performance basically does not change with the increase of the amount of silica. Comprehensive consideration, we think that the most suitable amount of silica in the defoamer should be about 1.3%.
3. The effect of the amount of polyether silicone oil on the performance of the defoamer
Polyether silicone oil itself has defoaming and antifoaming properties, and can produce synergistic effects with methyl silicone oil/modified silica. Fix other conditions unchanged, add polyether silicone oil and change its dosage, and observe the defoaming effect of the defoamer Performance, experimental results: the defoaming effect of pure methyl silicone oil/white carbon black emulsion is not the best. After adding polyether silicone oil, within a certain dosage range, the defoaming time of the defoamer becomes shorter as the dosage increases, and It is beneficial to prolong the anti-foaming time. In addition, the stability of the emulsion and its dispersibility in water become better with the increase of the amount of polyether silicone oil. The synergistic effect between the components makes the defoaming effect of the defoamer significantly improved. However, when the amount of polyether silicone oil exceeds 20 g (accounting for 10% of the total mass fraction of the emulsion), it will lead to the hydrophilicity of the defoamer components. The property of polyether silicone oil is greatly increased, and it is easy to disperse in the foaming liquid and reduce the antifoaming property. Therefore, the appropriate dosage of polyether silicone oil is about 10%.
4. The effect of compounding of emulsifier and its dosage on the performance of defoamer
Emulsifier is one of the key factors in the preparation of emulsion-type silicone defoamers. Methyl silicone oil is difficult to emulsify. In order to make the emulsifier can emulsify and disperse well, the H LB value of the emulsifier and the H LB value of the silicone oil should be considered first. (approximately 8-11) is close, and secondly, the foaming power of the emulsifier should be considered to be small, and the affinity between the emulsified system and the emulsifier's hydrophobic group should also be considered. Usually, ionic emulsifiers such as sulfonates , sulfuric acid esters, etc. have varying degrees of foaming effect, while Span-type and Tween-type non-off-type emulsifiers have better affinity with methyl silicone oil, and have low foaming performance, so this study uses Span-80 and Tween- 80 for compounding. The defoaming performance of the defoamer when the compound emulsifier has different H LB values is shown in Table 4. It can be seen from Table 4 that when the emulsifier H LB value is about 10, the defoaming performance of the defoaming agent, centrifugal Good stability and dispersibility in water.
Fixing other conditions and the ratio of emulsifier Span-80 to Tween-80 are unchanged, and investigating the influence of the amount of compound emulsifier on the performance of the defoamer, the experimental results: the amount of emulsifier is too small, the emulsion of the defoamer is unstable, It is easy to delaminate. If the amount of emulsifier is too large, the stability of the defoamer emulsion will increase, but the defoaming effect will decrease. This is caused by two factors: one is that the amount of emulsifier is too large, resulting in too small emulsion particles, so that the defoamer The speed is reduced; the second is that the amount of emulsifier is too much, which increases the stability of the emulsion, so that the emulsion particles cannot capture bubbles and lose the defoaming performance. When the amount of compound emulsifier is less than 6%, the stability of the defoamer emulsion increases with the compound The increase in the amount of emulsifier increases, and the defoaming performance is enhanced; when the amount of compound emulsifier is greater than 6%, the stability of the defoamer does not change with the amount of change, but the defoaming performance decreases. Experiments have proved that the compound emulsifier The defoaming effect of the defoaming agent is better when the dosage is about 6%.
5. Effect of thickener
In order to improve the stability of the emulsion, adding a thickener is an effective way. Commonly used thickeners include sodium methyl cellulose, ethyl cellulose, polyethylene glycol, sodium alginate, and the like.